Comprehending Porosity in Welding: Exploring Causes, Effects, and Avoidance Techniques
As experts in the welding market are well conscious, recognizing the causes, impacts, and avoidance strategies related to porosity is vital for attaining durable and dependable welds. By diving right into the origin causes of porosity, examining its detrimental impacts on weld top quality, and discovering effective prevention techniques, welders can enhance their knowledge and abilities to produce top quality welds continually.
Usual Reasons For Porosity
Contamination, in the kind of dirt, grease, or corrosion on the welding surface, creates gas pockets when heated up, leading to porosity in the weld. Improper securing occurs when the shielding gas, frequently used in procedures like MIG and TIG welding, is unable to fully protect the liquified weld swimming pool from reacting with the bordering air, resulting in gas entrapment and subsequent porosity. In addition, inadequate gas insurance coverage, typically due to incorrect flow rates or nozzle positioning, can leave parts of the weld unsafe, allowing porosity to create.
Results on Weld Quality
The existence of porosity in a weld can dramatically endanger the overall high quality and stability of the welded joint. Porosity within a weld develops gaps or dental caries that compromise the framework, making it a lot more susceptible to fracturing, deterioration, and mechanical failing.
Additionally, porosity can hinder the effectiveness of non-destructive testing (NDT) techniques, making it challenging to find various other flaws or suspensions within the weld. This can bring about considerable safety worries, specifically in important applications where the structural stability of the welded components is critical.
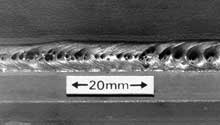
Prevention Techniques Introduction
Provided the harmful impact of porosity on weld quality, effective avoidance methods are crucial to keeping the structural honesty of welded joints. In addition, picking the suitable welding criteria, such as voltage, present, and take a trip rate, can assist decrease the danger of porosity formation. By integrating these prevention techniques right into welding methods, the event of porosity can be dramatically minimized, leading to more powerful and more trusted welded joints.
Importance of Appropriate Shielding
Proper protecting in welding plays a critical duty in stopping climatic contamination and guaranteeing the integrity of welded joints. Shielding gases, such as argon, helium, or a mixture of both, are commonly made use of to secure the weld pool from reacting with components in the air like oxygen and nitrogen. When these reactive elements enter call with the hot weld pool, they can cause porosity, leading to weak welds with lowered mechanical residential properties.
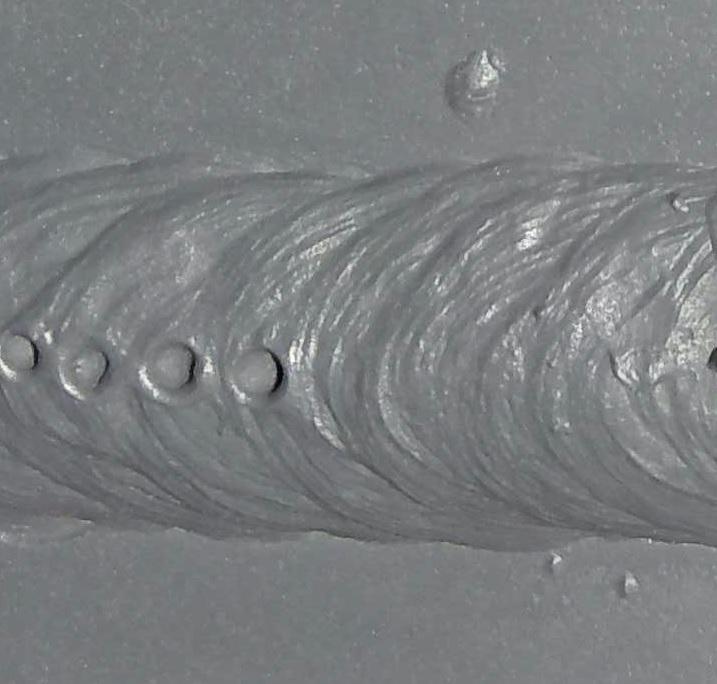
Insufficient shielding can cause numerous issues like porosity, spatter, and oxidation, compromising the structural honesty of the over here bonded joint. As a result, sticking to appropriate protecting techniques is crucial to generate top quality welds with minimal defects and make certain the longevity try this web-site and reliability of the bonded parts (What is Porosity).
Tracking and Control Methods
Exactly how can welders effectively monitor and manage the welding process to make sure optimal outcomes and prevent defects like porosity? By continually keeping an eye on these variables, welders can identify inconsistencies from the excellent problems and make prompt adjustments to protect against porosity formation.

In addition, applying proper training programs for welders is important for keeping an eye on and controlling the welding procedure successfully. What is Porosity. Educating welders on the relevance of keeping regular specifications, such as appropriate gas shielding and take a their explanation trip speed, can assist avoid porosity concerns. Routine assessments and certifications can likewise ensure that welders excel in tracking and managing welding processes
Additionally, making use of automated welding systems can boost monitoring and control capabilities. These systems can specifically manage welding specifications, lowering the probability of human mistake and making sure constant weld high quality. By incorporating advanced monitoring innovations, training programs, and automated systems, welders can properly check and manage the welding procedure to decrease porosity defects and attain high-grade welds.